Whether displaying a company brand or a visual user interface, in most modern graphics, more and more customers require color complexity beyond the capabilities of silk-screening or pad printing. When you break down these images, there may be as many as 50+ color hues in a gradation, resulting in a complex, colorful appearance. Due to the very complex color systems used in digital printing, custom injection molders with digital printing equipment can deliver complex graphics. In the past, it wasn’t possible with the old marking systems. Digital printers offer the desired complexity and the freedom to choose an unlimited number of color schemes, enabling today’s injection molding companies to put that on a plastic part.
Let’s discuss a few frequently asked questions we hear at Ferriot about digital printing and how it compares to other branding methods like pad printing.
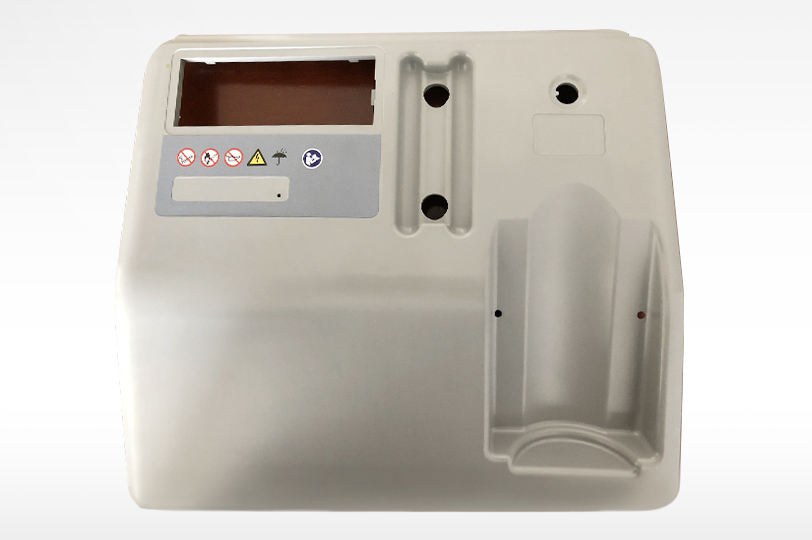
What problems does digital printing help solve compared to other methods, like pad printing?
Digital printing excels in a couple of areas over other branding machines, like pad printers. Applying complex designs to injection molded parts is where digital printers excel. If you’re familiar with silk-screening or pad printing, you know they’re limited in the number of colors they can handle. Most pad printing operations have four colors at a time capacity. When pad printing, there’s a cut steel template in the shape of the required image design, and it is recessed to hold ink. And then, that ink transfers via silicone pad to a part, and it imprints just that color of ink. There’s no mixing. The main advantage of digital printing over pad printing is that it allows you to print a more complex multicolor image in a higher resolution.
Bottom line: Pad printing is a great branding approach for monochromatic company logos or graphics in one or two colors. It’s fast, and it’s simple. However, once you get outside of one or two colors, using pad printing over digital printing doesn’t make sense anymore.
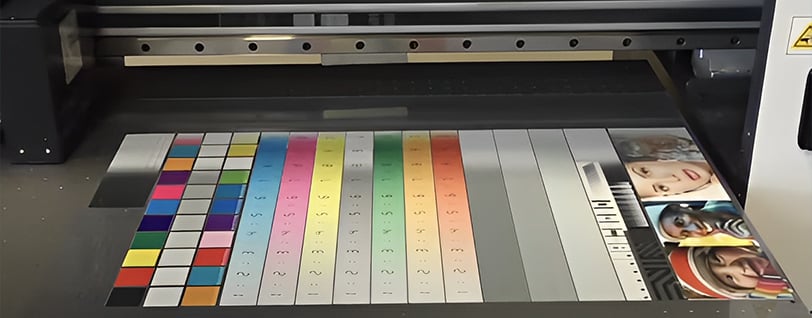
When comparing pad printing and digital printing, is there a difference in wearability, durability, or longevity? Or are they about the same?
They are comparable in wearability, durability and longevity, but it is dependent on the substrate. While pad printing technology is a lot older and proven over time, digital printing technology is moving along at a pace proving comparable, if not superior, quality. One advantage of the digital printer is if you need weather and UV sunlight resistance, the digital printer can easily apply protective clear coatings via the print carriage, all within the same print cycle. This approach enables the application of different protective coatings on top of the digitally printed artwork to add the necessary protection required, thus saving process time.
Ultimately, it comes down to the substrate and intended use of the finished product while meeting the customer’s specifications. The devil is in the details, and custom injection molders must address these requirements on a case-by-case basis. There is little that digital printers cannot do that is currently possible with pad printing, including medical equipment, which must adhere to strict requirements and be incredibly resistant to chemicals. Because medical equipment is wiped down and sanitized all the time, we’ve managed multiple medical applications with digital printing that have held up to their standards.
While different inks exist for particular applications, more than 95% use the same basic digital printer inks. In some applications, providing additional chemically resistant protection or another quality like UV protection requires an overcoat to the standard inks. While medical equipment, outdoor kiosk, or the frame at a gas pump all have different exposures or elements that could cause the printing to experience degradation over time, the overcoat of the standard inks is essential to define.
There are specialized inks for specific substrates. Another example is when a metallic sheen is required. Some inks include small metallic pieces that add sparkle when applied to the enclosure. That’s decorative, not protective, but requires custom inks to achieve the desired effect.
What is one of the biggest problems that you can solve with digital printing of injection molded parts?
The biggest challenge is the number of colors needed and the complexity of the print design. Using digital printing saves significant setup time when multiple colors are required. Each color set up occurs separately when using limited or outdated equipment—couple that with many pad printing machines having a four-color limit. There are eight color pad printers, but the operator prepares and prints each color separately. Additionally, each ink must dry before applying the next color.
Digital printing eliminates the bulk of the setup and drying time—the injection molded part inserts in the machine, and you get a finished part out. No staging parts between the color pads is needed. Using the digital printing approach increases the throughput compared to pad printing. Quicker turnaround is a huge advantage.
While it is possible to do two colors at a time with pad printing, it becomes problematic depending on the kind of ink because some bleeding occurs when printing wet ink on top of damp ink. Whether or not to attempt two colors at a time must be carefully considered on a part-by-part basis. Do the colors touch? Will the colors look good together? Or will the inks bleed together, resulting in fuzzy transition lines across the part? These problems are avoidable with digital printing.
Digital printing’s primary advantage over pad printing is the ability to lay down multicolor graphics without smudging, smearing, or bleeding together. Even when the graphics are pretty complex, the digitally printed parts are UV cured within the printer. Finished pieces come out fully cured to the touch as soon as the cycle’s over. Put another way, parts are ready to be handled once the print cycle is done.
Are there any cost advantages or disadvantages of going digital versus pad printing?
If you compare apples to apples, say the same simple one- or two-color graphic, pad printed versus digitally printed, the pad printer would be faster because of the simplicity of it. But the digital printer is far more efficient in ink usage because there’s no wasted material, which becomes even more critical as the complexity of the printed graphic increases.
Why? When pad printing, you must catalyze ink, i.e., take raw ink, and put in all components that may give it the properties it needs to adhere to the plastic parts. And, once you’ve catalyzed an ink, you’re on a time limit because the ink will go bad within an allotted period. Any ink that isn’t used cannot be saved or recaptured; it goes in the trash. There are some savings in raw materials with digital printing, just because it’s a more efficient application for ink usage. Digital printing is a greener technology because it reduces potential waste.
What is the size of the digital printing area compared to pad printing?
While digital printing has cost advantages when printing complex graphics, the print size is another significant factor.
The digital print area itself is relatively large—approximately 42 by 24 inches. Pad printing doesn’t provide quite as large an area. Typically pad printing is a one- or two-up operation; the fixtures don’t hold more than one to two parts, and the printer is set up to “mark the part” within its scope or stroke of the pad.
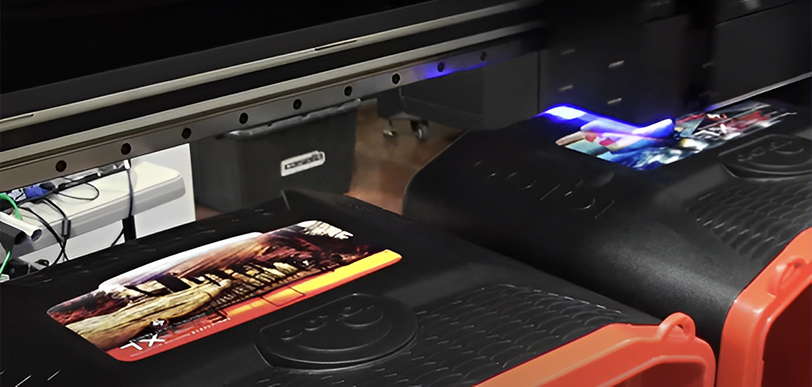
Conversely, digital printers have the advantage of being able to include as many parts as will fit within the print area and print all of them at the same time. So, digital printing can do more parts at once or even larger parts with larger print areas than with pad printing. Being capable of printing more extensive graphics or many more parts at once provides more flexibility for our customers.
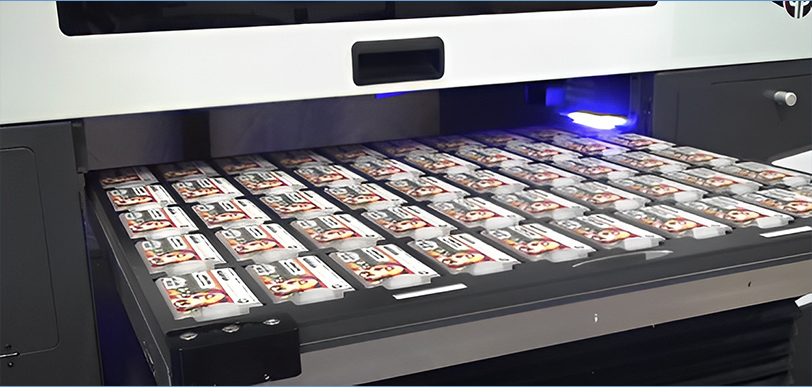
Ready to Elevate Your Injection Molded Parts with Digital Printing?
Discover the game-changing benefits of digital printing for injection molded parts. Say goodbye to limited color options and added labor cost due to lengthy setup times. With digital printing, you’ll enjoy unmatched complexity, vibrant multicolor designs, and efficient ink usage. Experience quicker turnaround, reduced waste, and a greener approach. Step into the future of branding and graphics – choose Ferriot’s digital printing for your injection molded parts today. https://www.ferriot.com/request-a-quote/
Learn more:
- Value Added Services > Painting and Decorating > Digital Printing
- Why Use Pad Printing to Add Your Brand to Injection Molded Parts?
- 3 Common Pad Printing Problems and How to Troubleshoot Them
- Pad Printing Services: 3 Common Problems to a Centuries-old Process & 3 Simple Solutions
Some images included in the blog are sourced from Ferriot’s vendor, Engineered Printing Solutions.